Inventory orders are for all items the company purchases.
On the main menu go to Admin > Inventory > Purchase Orders. This is where you view and manage all purchase orders.
From the inventory board you can view that status of all orders and create new inventory orders.
You can click the dropdown arrow next to the order number to show additional options. You can view the PO details, enter the supplier invoice, receipt the goods, update the order, change the order status and view the PO history:
Clicking the ‘eyeglass’ will open up the order details. Here you can print or email the order as well as ‘Confirm Goods Receipt’:
All orders can be tracked by their statuses. You can see the status from the board or within the order details screen:
From either of the boards, you can filter on what statuses are shown by using filters:
Make the filters you require ‘green’ by clicking on them. Only orders that are on any of the selected statuses will show:
Create a PO from the Inventory Item
To create an Inventory PO from the Inventory Item screen, go to Admin > Inventory > Items:
The inventory list will show. Use the ‘Search’ field to find the required item:
Click the ‘dropdown arrow’ icon to show the action list and select 'Create Purchase Order':
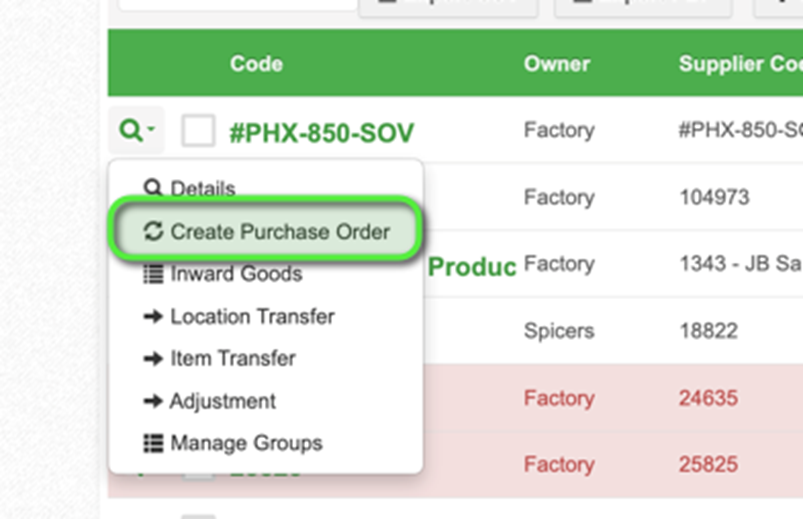
This will open the purchase order modal. Select a supplier and add the item and quantity required as well as the delivery details. Create the IPO and email to supplier. The IPO will now show on the board.
Create a PO from within the job 'Stock Pick' screen
You can create a stock PO from within a job by clicking ‘Stock Pick’ from the action list:
Also, from the IQ digital job bag, there is an ‘Inventory Pick’ option:
Both of the above options open the ‘Picking List’ screen. From here click the ‘Create Purchase Order’ icon:
This will open the purchase order modal. The supplier and item will already be pre-selected. Add the item and quantity required as well as the delivery details. Create the PO and email to supplier. The PO will now show on the board.
Receipt an Inventory Purchase Order
Fully Receipt IPO
From the ‘Inventory Purchase Orders Board’, you can set the filters to only show you orders on 'Awaiting Goods'. When the order arrives, select the ‘Receipt’ option from the eyeglass dropdown:
This opens the purchase order. The ‘Actual Quantity’ field is used to confirm the qty received. If the qty is correct click the ‘Confirm Goods Receipt’ button:

When an Inventory Purchase Order is generated, the ‘Location’ is set to receipt the quantity into the default location set against the item.
This can be changed via the location dropdown:
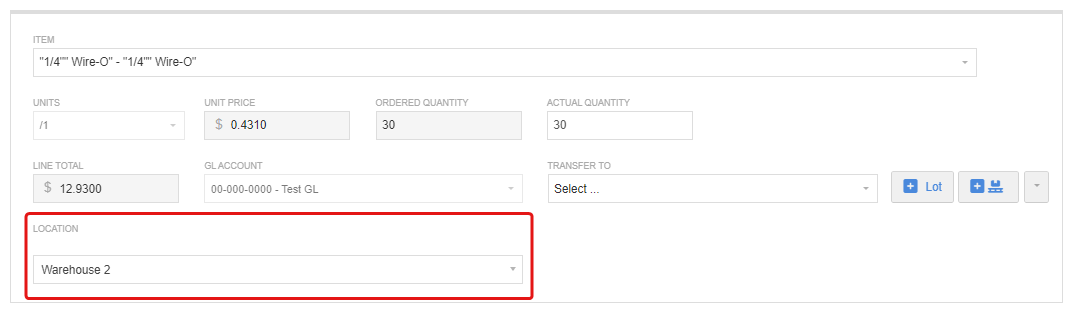

Clicking the location selector will display any additional locations linked to the item:
Part Receipt IPO
If the order has only been partially received, override the actual quantity to reflect what has been received and click ‘Confirm Goods Receipt’:
This will then create an additional IPO using the remaining quantity with a suffix at the end (-1):
The remaining quantity can then be receipted against this IPO:
If the remaining quantity is not going to be delivered for any reason, just cancel this order by changing the status:
Paper Based Inventory Orders
Paper stock can be setup many different ways. Some stocks can be ordered in packs, weight or area-based units.
When a stock has multiple inputs like this, you will see additional quantity fields. These will vary depending on how your paper stock is setup:
EXAMPLES:
Note:
Display of the below is controlled by the internal IQ setting: Advanced Stock
Quoting & Ordering Option

Pack Quantities
This stock is priced per /1000 and charged per
sheet:
When creating an inventory purchase order, you will see two quantity fields:
Ordered Quantity – this number represents the number of /1000 packs ordered
Total Unit Quantity - this number represents the total number of sheets. It multiplies the unit quantity by the ordered quantity:

You can enter a quantity in either field and it will auto update the other.
MSI/ft
In this example we have a stock ordered in MSI and charged per ft:
When creating an inventory purchase order, you will see two quantity fields:
Ordered Quantity – this number represents the number of MSI ordered
Lineal Quantity - this number represents conversion of the stock size into lineal feet:
CWT/lb
In this example we have a stock ordered in CWT and charge per lb:
When creating an inventory purchase order, you will see two qty fields:
Ordered Quantity – this number represents the number of CWT ordered
Total Unit Quantity - this number represents conversion of the CWT into lb:
Purchase Order Cancellation Email
This functionality enables email notifications to be sent to a supplier when a Purchase Order has been cancelled in printIQ. The setting ‘Purchase Order Cancellation Email’ has three options:
• Skip Email
• Automatically Email
• Prompt Before Email
When Skip Email is configured, an email will never be sent to the supplier on PO cancellation
Automatically Email
When ‘Automatically Email’ is set, a cancellation email is sent to the supplier automatically once a PO has been set to the cancelled status. The email is sent as soon as the status is changed and a prompt will not appear on-screen.
Prompt Before Email
When ‘Prompt Before Email’ is configured, a pop-up appears on screen after the status of the PO has been updated to Cancelled, and before the email is sent. This gives users the option to send the cancellation or not. The pop-up will display the email address and name of the supplier who the email will be sent to. Users must click ‘Send Email’ to send the cancellation email or ‘Don’t Send’ to stop the email from being sent out:

The 'Purchase Order Cancellation Email' setting exists at an instance, site and customer level.
Email Templates