Departments
The ‘Capacity Planning’ board can be separated into ‘Departments’ to make navigation easier.
From a production management point of view, you can select an overall department view. This will show all machines linked to that department for the specified ‘View’ day/date range:
Staff can view and use as ‘work to’ lists by filtering to individual presses/machines:
You can also filter down to day or date ranges, by the ‘Start’ time for the day, machine ‘capacity’ or filter down to a single job:
On a press, the department is set against the press ‘Department’:
On any machines, it is also set against the ‘Department’:
‘Departments’ can be created and moved into a production order as required:
For any press or machine to show on the capacity board, it must have the ‘Schedulable’ checkbox ON:
You can also set the ‘work hours’ against each press or machine:
At a press level, as we can have a separate ‘press’ by work type (Sheetwork, Perfect, Work/Turn, Work/Tumble), you consolidate the press into the one ‘planning press’ by setting the ‘Capacity Plan As’ option:
For additional information on setting up presses for Capacity Planning, see KB documents below:
Capacity Planning - Part 1 - Planner
Related Machine - Allocating Jobs to Machine
Planning Admin
Under the ‘Planning Admin’ screen there is tabs for configuring ‘Groups’, ‘Settings & Tolerances’ and ‘Department Filters’:
Planning 'Groups':
Planning Groups are used to enable you to move an operation between machines. Groups can be created and machines linked to groups can be viewed.
Link ‘like’ machines to the same planning group so you can drag/drop operations onto a different machine than the quoted machine.
At a machine level, the ‘group’ can be selected:

Use the ‘None’ option if the machine is unique. This will stop the operation from being dragged onto any other machine
If you try drag an operation onto a machine that is not linked using the planning groups, you will be flagged with an ‘Incompatible Machine type’ message:
Settings & Tolerances
Under the ‘Planning Admin’ screen inside the ‘Settings & Tolerances’ tab, there are global settings than can be configured:
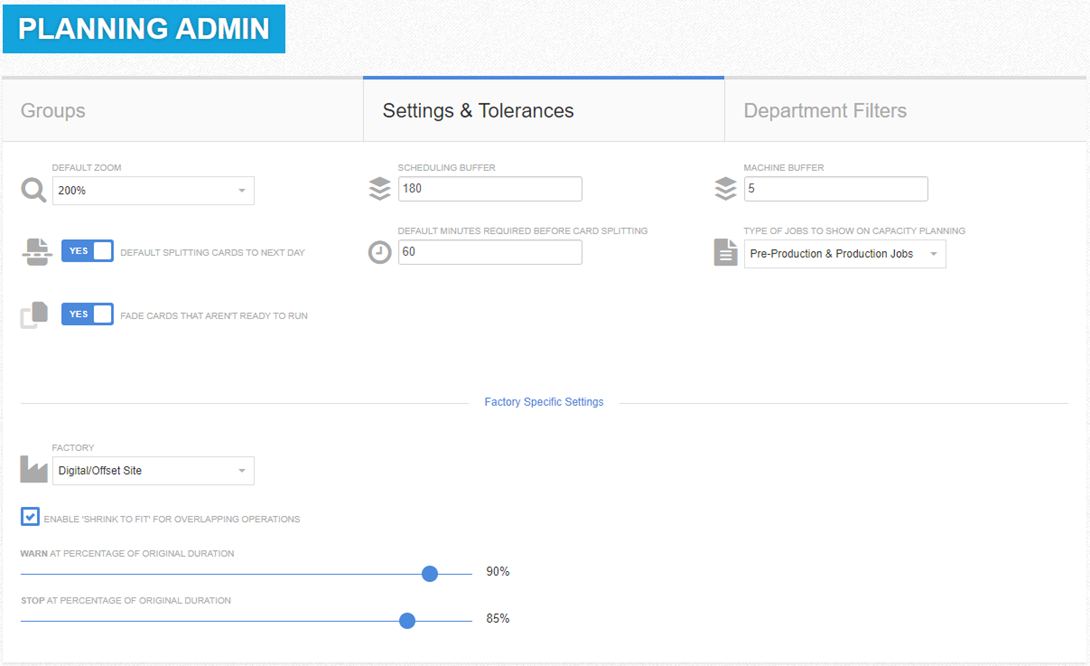
Default Zoom
The default zoom % can be defined. The standards is set at 100%
Buffers
Default ‘Scheduling Buffer’ between individual ‘job’ operations (such as 3 hours between operations on the same job). This is applied when using the ‘Auto Plan’ options in printIQ.
Default ‘Machine Buffer’ between operations by machine (such as 5 mins between individual operations on the one machine). This is applied when using the ‘Auto Plan’ options in printIQ.
Auto Splitting
There are default settings for ‘Auto-Splitting’ of job cards. The setting can be turned ON/OFF and a minimum time allowance for auto splitting (for example 30min minimum remaining required before the auto split will activate).
Type of jobs to show on Capacity Planning
This setting lets you filter what job status options show as available for capacity planning. The options are:
Pre-Production and Production Jobs – This includes all jobs on a active production based status
All Non-Complete Jobs – This will show all jobs in printIQ other than jobs on a status of ‘Complete’, ‘Cancelled’ or ‘Finished Production’.
Fade cards that aren't ready to run
If this setting is on and you have an operation that’s planned but current locked on the job details screen the card will be faded out on capacity planning. This is a visual clue to the user that the operation is not ready to be started as a previous operation is still incomplete.
Shrink to Fit
Allows enabling the option to auto shrink operation to fit into open gaps. You ca set shrink allowances and warning triggers.
Department Filters
You can setup advanced filtering via ‘Department Filters’:
A list of all configured ‘departments’ will show. Click the ‘Edit’ button to configure what filters will be available on the Capacity Planner Board.
In this example, for ‘Offset Presses’ we have set the available filters to be ‘Stock, Stock Size, Process Front and Process Back’:
This will view as:
For ‘Folders’ we have a different set of filter options of ‘Finish Size’ and ‘Operation’:
This will view as:
Other Settings
These require a support team member to alter. Delete old cards – A number of ‘days’ can be set specifying when old jobs are removed from the capacity planner boards.
These function helps with board loading performance.