A raw material can be created and added to a 'Material Set'.
Material Sets' are then linked to pricing component lines within operations, so they are included in quoting for cost and inventory purposes.
This is managed from ‘Material Admin’ under ‘Equipment’ in the ‘Configure the Factory’ screen.
Add new Material
To begin creating a new 'Raw Material', click the ‘+’ button.
A material creation dropdown will show. This is where you configure the details and pricing:
In this example we are creating a roll of gloss laminate:
Some fields of note:
- Inventory Location - Choose a location for the material. This can be something general like the name of your company or if you have a full inventory warehouse configured, you can specify the exact location where this stock will be stored.
-
Code - A code will be auto generated by IQ but it is always best to use a code that actually relates to the material as this 'code' is what you select inside the operation component screen to link so the clearer the name the easier it is to select later.
Maximum code length is 100 characters
- Description - Enter the full description of the material here.
- Calc type - Select the calculation type that best relates to the material being created (see further down in documentation for more info). In this case we are selecting 'Roll applied to Sheets' as this will look at the sheet (or Roll) size of the material being printed on to calculate the number of metres required to laminate the printed job.
- Extra mm per sheet - When some calculation types are selected, additional options are shown. In this case we have the option to enter an extra mm per sheet to allow for the gap between sheets when laminating. Enter a number here for the gap size or add 0 if you do not want to add any extra.
- Roll Width mm - This is another option triggered by the calculation type selected. Here we enter the width of the roll. This is used to determine what side of the sheet will need to be used as the leading edge. This is then used to calculate the correct number of metres required to produce the job.
- Order in units of - Select the quantity that the item is ordered in. In the case of a roll, we enter the cost of a single roll. NOTE: If you select a charge unit type of /Roll or a length/area based unit type, you will get an extra field – Order ->Charge Unit Conversion Factor. This allows you to enter the charge cost. For example, a roll of 50metres at $100 per roll, you would make the charge unit /1 to charge per metre. 100/50=$2 per metre. This will also flow through to the purchasing of the item. If you order in 1 roll, on receipt of order, 50 metres will be added to inventory to allow for accurate stock pick/inventory management.
- Charge in units of - With rolls, a unit selection of /1 equals either 1 linear metre / foot, or 1 square metre / foot, dependent on calculation type. Enter the price per metre.
- Default Supplier - Select the default supplier the item is ordered from. Once the item has been created, you can add additional suppliers from within the inventory section of IQ.
- Owned by - You can specify if the material is owned by the 'Factory' (you), 'Supplier' or 'Customer'.
- Weight - You can enter a weight for the item 'per unit'.
- Quantity on Hand - If you already have stock on hand when you create the material, you can enter the qty here.
Checkboxes:
- Awaiting Delivery - This is just a flag you can check on if when creating the material and say the customer is sending it directly to you, you can mark it as awaiting delivery and you can filter this on the inventory screen for tracking purposes.
- Manage Stock Levels - Check this on if you want to manage the stock levels of the material. This allows you to do a 'pick' on the item from within a jobs 'Stock Pick' screen.
- Active - Turns the item from 'Active' to 'Inactive'.
At the top of the screen are some additional tabs:
Modifying Material Sets
Material Sets - When a material is created, a material set is generated using the items 'code.
You always need the material linked to at least one material set as the material set is what you link to within a pricing component line:
If an operation requires multiple materials, you can create your own material set (enter a name and 'add').
You can then go into multiple materials and add that new material set to its list.
One material can be linked to as many different materials sets as you require.
Price Modifier - If you want the materials on this set to have a default 20% added to their price, you can enter '1.2' into this field
Quantity Modifier – This field allows you to set the quantity per item of materials required for the material set.
In the below example, we have a material setup to be ordered ‘Per Unit’:
On the material set, we have configured ‘packs’ of screws.
The quantity required can be set/selected depending on the item being quoted.
Against the operation component, we have 3 options linked to each material set:
On the quote you can select the required option:
The material will multiply per unit ordered and display throughout printIQ:
Calc Types
Sheet area {AreaLongUnitName}
Area of All Sheets, ignoring press spoils
Finish area {AreaLongUnitName}
Area of the finished job
Print Sheets
Count of all sheets
Operation Price
Quantity of 1
Per Unit
Job Quantity
Per Page
Job Quantity * Number of Pages
Job - {LengthLongUnitNameSingular} width
Job Quantity * Job Width
Job - {LengthLongUnitNameSingular} depth
Job Quantity * Job Depth
Job - {LengthLongUnitNameSingular} height
Job Quantity * Job Height
Job - {AreaLongUnitNameSingular} area
Job Quantity * Job Area
Job - {VolumeLongUnitNameSingular} volume
Job Quantity * Job volume
Job - {WeightLongUnitNameSingular} weight
Job Quantity * Job Weight
Job - perimeter
Job Quantity * Job Perimeter including any inner 'tiling'
Flat Per Page
Pages per item
Sheet - {LengthLongUnitNameSingular} length
Total Sheet Length + Any Defined Extra Per Sheet
Sheet - {LengthLongUnitNameSingular} width
Total Sheet Width + Any Defined Extra Per Sheet
Roll Applied to Sheets
Roll Applied to Items
Calculation applies to both items and sheets, ‘items’ applies to individual items, ‘sheets’ to the whole printed sheets
Take the Material Width Defined
If the material width covers the sheet across the long edge (MatWidth > LongEdge)
material goes across the long edge, length is (ShortEdge + extra) * Quantity
else
material goes across the short edge, length is (LongEdge + Extra) * Quantity
Roll Applied to Sheets w/ slit
Roll Applied to Items w/ slit
Calculation applies to both items and sheets, ‘items’ applies to individual items, ‘sheets’ to the whole printed sheets
Take the Material Width Defined
If the material has no overhang over the long edge (MatWidth >= LongEdge)
material goes across the short edge, length is (LongEdge + Extra) * Quantity
else
material goes across the long edge, length is (ShortEdge + extra) * Quantity
Plate Finish Area {AreaLongUnitName}
Job Area * Number of Plates * NUp
Plate Sheet Area {AreaLongUnitName}
Sheet Area * Number of Plates
Plate per unit
Number of plates
Tile - Join {LengthLongUnitNameSingular}
Length of all joined edges for tiles
Shape Output
Reference a Calculated Shape output by name, this value * quantity
Items Along Perimeter
Items Along Component Defined Length
These use the same calculation, Perimeter is Width * 2 + Depth * 2,
Component Defined uses Width * WidthMultiplier + Depth * DepthMultiplier from the component record
Options are roundup or round down and apply to total or apply to each edge.
if applying to all calculate how many items fit along the full length then round
Number of Items per unit = ROUND(((Width * WidthMultiplier + Depth * DepthMultiplier) / Gap)
else calculate and round each edge separately
Number of Items per unit = (ROUND(Width / Gap) * WidthMultiplier) + (ROUND(Depth / Gap) * DepthMultiplier)
Total Items = Number of Items * Quantity
You can set a default quantity to be added in addition to the calculated quantity.
Using the fields:
Extra total items - Sets an additional quantity to add to the calculation 'per item'
Extra items per edge - Sets an additional quantity to add to the calculation 'per edge' configured on a component (defined using component options 'Component Length Width/Depth Multiple')
Job - {LengthLongUnitNameSingular} from component
Job Width * ComponentWidthMultiplier + JobDepth * ComponentDepthMultiplier
Number of Packs
Material calculation based on the number of packs configured when using 'Packs' functionality on quotes
Job - Assembled Perimeter
Job Quantity * Job Perimeter excluding any inner 'tiling'
Notes on calc types
Calculation types below do not work with Job Based Operations:
- Sheet area {AreaLongUnitName}
- Finish area {AreaLongUnitName}
- Print Sheets
- Sheet - {LengthLongUnitNameSingular} length
- Sheet - {LengthLongUnitNameSingular} width
- Roll Applied to Sheets
- Roll Applied to Sheets w/ slit
- Roll Applied to Items w/ slit
- Roll Applied to Items w/ slit
- Roll Applied to Items
- Plate Sheet Area {AreaLongUnitName}
- Plate Finish Area {AreaLongUnitName}
- Plate per unit
- Cylinder Plate Area
Export/Import
You can use the Export and Import options to export all or a filtered set of materials from the Materials Admin board to CSV.
Details of the materials can be changed and / or the pricing updated before importing the CSV back into printIQ to update those materials.
[refer to the Bulk Materials Upload screen for a detailed description of the calculation requirements to set up the Calculation Types]
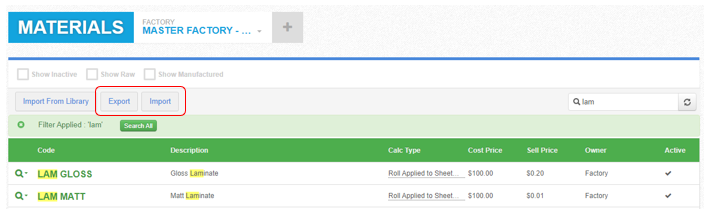
GL Account
The CSV also exports the inventory expense GL Account Code, if set on the Inventory Record.
Clearing the contents on the CSV (if set) and uploading would remove the expense GL accounts against that inventory record for the material.
Material Categories
Material categories are a comma separated list of category names in the CSV.
New categories will be added automatically and any existing categories on the material that are not on the CSV when it is re-uploaded will be removed from that material.
The material with three categories above shows up as...
Material Sets
Material sets are downloaded to the export CSV.
They are listed as comma separated values (when there is more than one material set defined)
Each material set in the CSV has three fields - Material Set Name, Price Modifier and Quantity Modifier...
The material with two Material Sets above displays as...