Creating Outsource Purchase Orders
At a job level, you can generate an outsource purchase order (OPO) for a ‘partial’ outsource (where selected operations are outsourced) or a ‘full’ outsource (where the entire production of the job will be outsourced).
This initial outsource can be set against the quote or added later at the job level.
In this example, we have quoted the operation ‘MACH DIECUT’ to be outsourced to an outside supplier:
Any job with a predefined outsource from the quote will display a ‘!’ warning flag next to the ‘Outsource’ tab:
Inside the ‘Outsource’ tab, click the ‘+ New purchase order’ button:
An outsource modal will drop in the front of the screen. The modal is broken into multiple sections:
The first section lets you select what you would like to outsource on the job:
Outsource Job:
This allows you to create a general outsource PO against the job. This is not linked to any ‘operation’ inside the job itself.
Outsource MACH DIECUT – Monastery Hill Bindery:
Any operation with an outsource pre-configured at the quote level, will show in this middle section. It will have the name of the operation along with the supplier’s name.
When selected, the screen will pre-populate with the details set against the quote such as the selected supplier, outsource description and price:
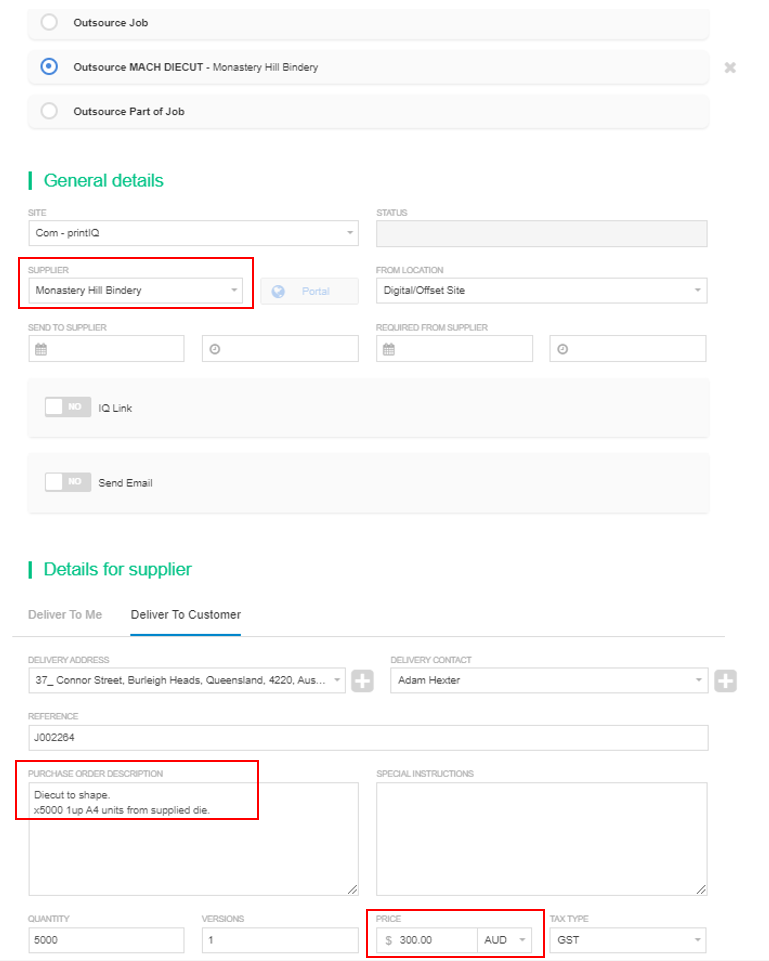
Outsource Part Job:
This option adds a field called ‘Select Operation’:
Here you can select one or more operations to outsource:
The selected operations will then show in the field:This will flag the selected operations in the job as outsourced:
This will flag the
selected operations in the job as outsourced:
Back on our example job, we select the pre-defined outsource operation for the die cutting at Monastery Hill Bindery:
This auto fills the ‘Supplier’. Next fill in the ‘Sent to Supplier’ and ‘Required from Supplier’ date and times:
You can select to send the outwork purchase order to the supplier via an email:
Lastly, select the delivery option of either ‘Deliver to Me’ or ‘Deliver to Customer’. Also check the description, details, and price:
Click ‘Save’ to generate the OPO:
The OPO is now created and will display in the jobs outsource tab:
The OPO will now display on the ‘Outsource’ board under its relevant status. This is where you can manage and track the status of the order:
Use the ‘Change Status’ option under the orders ‘eyeglass’ to update the status of the order as required:
Set the status to ‘Goods Sent’ when you are sending the job to your supplier:
Receipting Goods
Once the job returns to the factory, you can ‘receipt’ in by quantity. Click on the eyeglass and select the ‘Receipt’ option:
In the modal is a ‘Goods received’ section:
Enter the received qty and a note if required and click ‘Confirm Goods Received’:
The received qty will be logged (this can also be edited or removed):
This will also update the order status to ‘Goods Received’:
Once the supplier invoice has been received, the OPO status can be updated to ‘Invoice Received’:
From here, accounts can select to ‘Enter Supplier Invoice’:
The supplier invoice can be generated and exported into your accounts package:
Receiving Partial Quantity
You can receive partial quantities against an OPO. A log of all quantity received will display on screen:
The Outsource Board will also show the order as ‘Partially Received’ and show the received qty:
Supplier Portal
Your supplier will receive an email with a pdf file of the OPO attached. They will also get a link in the email to the printIQ ‘Supplier Portal’. The supplier does not require any login or password to access the portal.
In the portal they will have all the order details and relevant files. They can also send updates back to you via the ‘Supplier Dispatch’ section of the portal:
When you update the OPO to the status of ‘Goods Sent’:
That will update the status on your board:
This will also update the supplier portal to show the date and time you sent the items to them:
As the job progresses, at the suppliers side, they can fill out the dispatch options and ‘Submit Details’ back to you:
This will update the ‘i’ icon on the outsource board:
Hover over the icon to see the details:
Any delays or issues can be logged under the ‘Job Delayed’ section:
This will flag as a ‘warning’ on the outsource board:
Once the supplier has completed the job, they can update the relevant details and submit back to you:
This will again update your details with a history from the supplier:
The supplier portal includes the dispatch details and required date under the ‘Delivery’ tab:
Edit an OPO
You can ‘edit’ an existing OPO by clicking on the price button:
This opens the OPO modal where you can make the required changes and select to either ‘Save’ over the existing order; ‘Create New’ order or ‘Overwrite’ the existing order:
‘Overwrite’ will cancel the existing order and create a new purchase order with a new PO number to replace the old one.
As an example, this order was created as OPO000202. It has been updated multiple times via the ‘Save’ option and shows three OPO versions:
Using the ‘Overwrite’ option:
The OPO000202 has been cancelled and replaced with OPO000203:
Send Printed Product
Inside the OPO is a button ‘Send printed product’:
This is an internal reference section only, where you can record detail such as the courier used for the delivery to the supplier and their connote reference:
Purchase Order Approvals
When a user has a PO approval limit set against them via the below user setting:
When they generate a PO over their approval value, they will see a ‘Request Approval’ button in place of a ‘Save’ button:
They can still generate the OPO, but the status will default to ‘Awaiting Approval’:
The order will show on the Outsource board under the ‘Awaiting Approval’ status and filter:
A user with no approval limits can then open the order and click ‘Approve’:
This will update the OPO status to ‘PO Created’:
The order can now be sent to the supplier.
Outsource Purchase Order Approval History
This can be seen in the job’s history records:
Approval User Setup:
Approval amount is based off the user’s approval amount. The below setting must be applied:
Roles – Must have ‘Purchase Approver’:
User setting for ‘Purchase Order Auto-Approval Limit’ at the minimum cannot get set at a global level. You must have the ‘Edit’ slider checked ON: